రెగ్యులర్ మెయింటెనెన్స్ప్యాలెట్ బండ్లుభద్రత, ఉత్పాదకత మరియు పరికరాల దీర్ఘాయువును నిర్ధారించడానికి ఇది చాలా ముఖ్యమైనది. మీ సేవ చేయడం ద్వారాప్యాలెట్ జాక్స్క్రమం తప్పకుండా, మీరు ఆపరేటర్లను రక్షించడమే కాకుండా సామర్థ్యాన్ని పెంచుకోవడమే కాకుండా పరికరాల ఆయుష్షును కూడా విస్తరిస్తారు. ఇక్కడ, మీరు అవసరమైన చిట్కాలను కనుగొంటారుప్యాలెట్ బండ్లను సమర్థవంతంగా నిర్వహించడం, భాగాలపై దుస్తులు తగ్గించడం, మరమ్మతులను తగ్గించడం మరియు ఆపరేటర్ ఆరోగ్యాన్ని కాపాడటం.
నష్టాలను పరిశీలించండి మరియు మరమ్మత్తు చేయండి
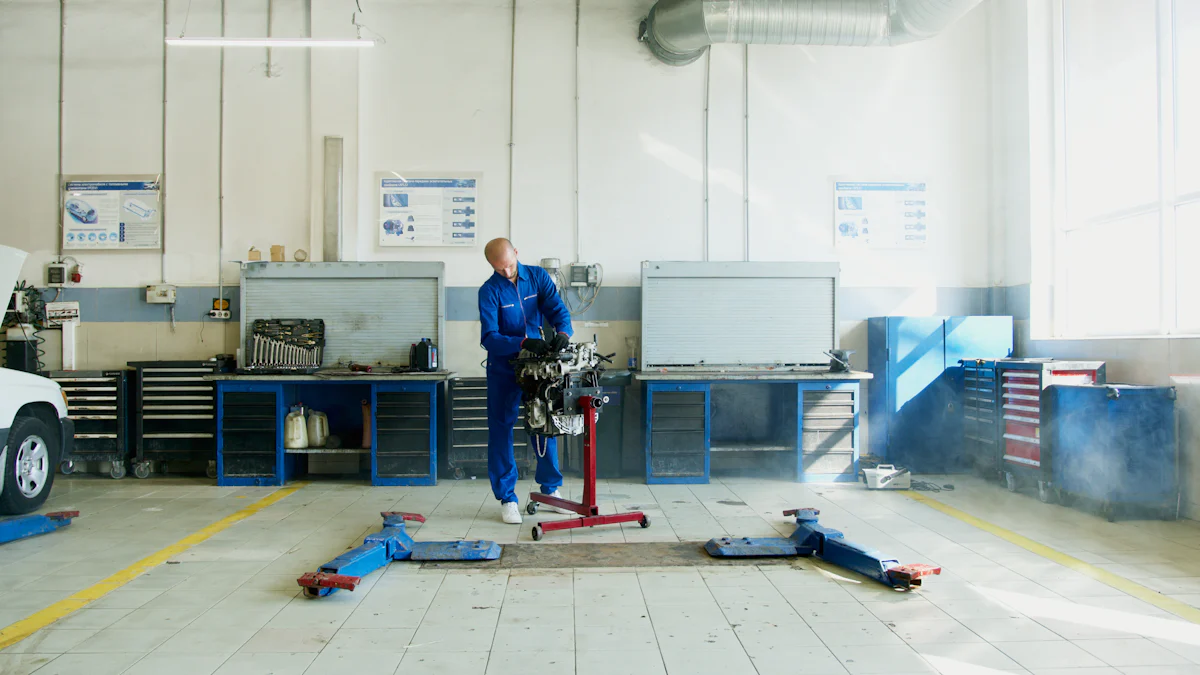
రెగ్యులర్ తనిఖీలు
రెగ్యులర్ తనిఖీలు కీలక పాత్ర పోషిస్తాయినిర్వహించడంలోప్యాలెట్ కార్ట్. నిర్వహించడం ద్వారారెగ్యులర్ తనిఖీలు, సంభావ్య సమస్యలను ప్రారంభంలో గుర్తించవచ్చు, ప్రధాన పనిచేయకపోవడం మరియు ఖరీదైన మరమ్మతులను నివారించవచ్చు. అది నిర్ధారిస్తుందిప్యాలెట్ జాక్స్సురక్షితమైన మరియు సమర్థవంతమైన ఆపరేషన్ కోసం సరైన స్థితిలో ఉన్నాయి.
చక్రాలు మరియు కాస్టర్లు తనిఖీ చేస్తోంది
చక్రాలు మరియు కాస్టర్లను తనిఖీ చేయడం సాధారణ నిర్వహణ యొక్క ప్రాథమిక అంశం. ఈ దశలో ప్రతి చక్రం మరియు కాస్టర్ను పూర్తిగా పరిశీలించడం జరుగుతుంది, అవి నష్టం లేదా అధిక దుస్తులు నుండి విముక్తి పొందాయి. దుస్తులు లేదా తప్పుగా అమర్చడం యొక్క ఏదైనా సంకేతాలను తనిఖీ చేయడం ద్వారా, ఆపరేటర్లు ఈ సమస్యలను వెంటనే పరిష్కరించవచ్చు, ఇది పరికరాల దీర్ఘాయువును పెంచుతుంది.
నిర్మాణ భాగాలను పరిశీలిస్తోంది
సాధారణ తనిఖీలలో మరొక కీలకమైన భాగం, యొక్క నిర్మాణ భాగాలను పరిశీలించడంప్యాలెట్ కార్ట్. నష్టం లేదా బలహీనత యొక్క ఏదైనా సంకేతాల కోసం ఫ్రేమ్, హ్యాండిల్స్ మరియు ఇతర నిర్మాణ అంశాలను అంచనా వేయడం ఇందులో ఉంది. సాధారణ తనిఖీల సమయంలో ఈ సమస్యలను గుర్తించడం మరియు పరిష్కరించడం ద్వారా, ఆపరేటర్లు నిర్వహించవచ్చునిర్మాణ సమగ్రతయొక్కప్యాలెట్ జాక్స్.
మరమ్మతులు చేస్తోంది
ప్రదర్శనసకాలంలో మరమ్మతులు అవసరంఉంచడానికిప్యాలెట్ కార్ట్ఉత్తమంగా పనిచేస్తుంది. ఏదైనా నష్టాలను పరిష్కరించడం లేదా వెంటనే ధరించడం వల్ల మరింత క్షీణతను నిరోధించవచ్చు మరియు పరికరాలు ఉపయోగించడానికి సురక్షితంగా ఉండేలా చూసుకోవచ్చు.
దెబ్బతిన్న భాగాలను మార్చడం
నిర్వహణను నిర్వహిస్తున్నప్పుడుప్యాలెట్ జాక్స్, దెబ్బతిన్న భాగాలను వీలైనంత త్వరగా భర్తీ చేయడం చాలా ముఖ్యం. ఇది ధరించిన చక్రం లేదా పగిలిన హ్యాండిల్ అయినా, దెబ్బతిన్న భాగాలను భర్తీ చేయడం వల్ల భవిష్యత్తులో మరింత విస్తృతమైన సమస్యలను నిరోధించవచ్చు.
నిర్మాణ సమగ్రతను నిర్ధారిస్తుంది
యొక్క నిర్మాణ సమగ్రతను నిర్వహించడంప్యాలెట్ కార్ట్దాని మొత్తం పనితీరు మరియు భద్రతకు కీలకం. అన్ని నిర్మాణాత్మక భాగాలు మంచి స్థితిలో ఉన్నాయని నిర్ధారించడం ద్వారా, ఆపరేటర్లు ప్రమాదాలను నివారించవచ్చు మరియు వారి పరికరాల ఆయుష్షును పొడిగించవచ్చు.
మీపై నష్టాలను పరిశీలించడానికి మరియు మరమ్మత్తు చేయడానికి ఈ అవసరమైన చిట్కాలను అనుసరించడం ద్వారాప్యాలెట్ జాక్స్, మీ పరికరాలు సజావుగా, సురక్షితంగా మరియు సమర్ధవంతంగా పనిచేస్తాయని మీరు నిర్ధారించుకోవచ్చు.
కదిలే భాగాలను ద్రవపదార్థం చేయండి
యొక్క ప్రాముఖ్యతసరళత
ఘర్షణను తగ్గించడం
ప్యాలెట్ బండ్ల కదిలే భాగాల మధ్య ఘర్షణను తగ్గించడంలో సరళత కీలక పాత్ర పోషిస్తుంది. ఇరుసులు మరియు కీళ్ళకు కందెనలను వర్తింపజేయడం ద్వారా, ఆపరేటర్లు ఆపరేషన్ సమయంలో ఎదుర్కొన్న ప్రతిఘటనను తగ్గించవచ్చు, ఇది సున్నితమైన కదలికలకు మరియు పరికరాలపై తక్కువ ఒత్తిడికి దారితీస్తుంది.
జీవితకాలం విస్తరించడం
సరైన సరళత ప్యాలెట్ జాక్లపై దుస్తులు మరియు కన్నీటిని తగ్గించడమే కాక, వారి ఆయుష్షును గణనీయంగా విస్తరిస్తుంది. ఇరుసులు మరియు కీళ్ళు వంటి కీలక భాగాలను క్రమం తప్పకుండా సరళత చేయడం ద్వారా, ఆపరేటర్లు అకాల క్షీణతను నిరోధించవచ్చు మరియు పరికరాల దీర్ఘాయువును నిర్ధారించవచ్చు.
రస్ట్ నిరోధిస్తుంది
సరళత యొక్క ముఖ్య ప్రయోజనాల్లో ఒకటి లోహ భాగాలపై తుప్పు ఏర్పడకుండా నిరోధించే సామర్థ్యం. తేమ మరియు తుప్పుకు వ్యతిరేకంగా రక్షిత అవరోధాన్ని సృష్టించడం ద్వారా, కందెనలు ప్యాలెట్ బండ్ల యొక్క నిర్మాణ సమగ్రతను నిర్వహించడానికి సహాయపడతాయి, ముఖ్యంగా తేమ లేదా తడిగా ఉన్న వాతావరణంలో.
కందెనలు రకాలు
సరైన రకాన్ని ఎంచుకోవడం
ఎంచుకోవడంతగిన రకం కందెనసమర్థవంతమైన నిర్వహణకు అవసరం. గ్రీజ్ లేదా ఆయిల్-బేస్డ్ సొల్యూషన్స్ వంటి వివిధ రకాల కందెనలు నిర్దిష్ట అనువర్తనాలకు తగిన ప్రత్యేక లక్షణాలను అందిస్తాయి. ఆపరేటర్లు వారి ప్యాలెట్ జాక్లకు చాలా సరిఅయిన ఎంపికను నిర్ణయించడానికి తయారీదారు మార్గదర్శకాలను సూచించాలి.
అనుకూలతను నిర్ధారిస్తుంది
ప్యాలెట్ బండ్ల కోసం కందెనలను ఎన్నుకునేటప్పుడు, నిర్మాణంలో ఉపయోగించే పదార్థాలతో అనుకూలతను నిర్ధారించడం చాలా ముఖ్యం. అననుకూల కందెనలను ఉపయోగించడం వల్ల కాలక్రమేణా భాగాల నష్టం లేదా క్షీణతకు దారితీస్తుంది. పరికరాల యొక్క అన్ని భాగాలలో ఎంచుకున్న కందెన ఉపయోగం కోసం సురక్షితంగా ఉందని ఆపరేటర్లు ధృవీకరించాలి.
అప్లికేషన్ యొక్క ఫ్రీక్వెన్సీ
సరళత అనువర్తనం యొక్క పౌన frequency పున్యం వినియోగ తీవ్రత మరియు పర్యావరణ పరిస్థితులతో సహా వివిధ అంశాలపై ఆధారపడి ఉంటుంది. పొడి లేదా ఘర్షణ సంకేతాల కోసం క్రమం తప్పకుండా ఇరుసులు మరియు కీళ్ళను పరిశీలించడం పున app పరిశీలన ఎప్పుడు అవసరమో నిర్ణయించడంలో సహాయపడుతుంది. స్థిరమైన సరళత షెడ్యూల్ను నిర్వహించడం సరైన పనితీరు మరియు దీర్ఘాయువుకు కీలకం.
ప్యాలెట్ జాక్లను నిర్వహించడంలో సరైన సరళత యొక్క ప్రాముఖ్యతను అర్థం చేసుకోవడం ద్వారా మరియు తయారీదారుల సిఫారసుల ఆధారంగా సరైన రకమైన కందెనను ఎంచుకోవడం ద్వారా, ఆపరేటర్లు పరికరాల పనితీరును మెరుగుపరుస్తారు, అకాల దుస్తులు ధరించవచ్చు మరియు వారి విలువైన ఆస్తుల జీవితకాలం పొడిగించవచ్చు.
క్రమం తప్పకుండా శుభ్రం చేయండి
శుభ్రపరిచే పద్ధతులు
రెగ్యులర్ మెయింటెనెన్స్ప్యాలెట్ బండ్లుసరైన పనితీరు మరియు దీర్ఘాయువును నిర్ధారించడానికి శుభ్రపరచడం ఉంటుంది. సమర్థవంతమైన శుభ్రపరిచే పద్ధతులను అమలు చేయడం ద్వారా, ఆపరేటర్లు శిధిలాలు మరియు కలుషితాలను నిర్మించడాన్ని నిరోధించవచ్చు, అది వారి కార్యాచరణను రాజీ చేస్తుందిప్యాలెట్ జాక్స్.
శిధిలాలను తొలగించడం
నుండి శిధిలాలను తొలగించడంప్యాలెట్ కార్ట్శుభ్రపరిచే ప్రక్రియలో కీలకమైన దశ. ఆపరేటర్లు పరికరాలపై పేరుకుపోయే ఏదైనా ధూళి, ధూళి లేదా వదులుగా ఉన్న కణాలను క్రమం తప్పకుండా పరిశీలించి క్లియర్ చేయాలి. ఈ సరళమైన పని అడ్డంకులను నివారించడంలో సహాయపడుతుంది మరియు మెటీరియల్ హ్యాండ్లింగ్ పనుల సమయంలో సున్నితమైన ఆపరేషన్ను నిర్ధారిస్తుంది.
ధూళి మరియు కలుషితాలు శుభ్రపరచడం
కనిపించే శిధిలాలను తొలగించడంతో పాటు, ఆపరేటర్లు ధూళి మరియు కలుషితాలను పరిష్కరించాలి, అది శుభ్రతను ప్రభావితం చేస్తుందిప్యాలెట్ జాక్స్. బ్రష్లు లేదా వైప్స్ వంటి తగిన శుభ్రపరిచే పరిష్కారాలు మరియు సాధనాలను ఉపయోగించడం, వివిధ ఉపరితలాల నుండి ధూళి మరియు గ్రిమ్ను పూర్తిగా తొలగించడానికి అనుమతిస్తుంది. స్వచ్ఛమైన వాతావరణాన్ని నిర్వహించడం ద్వారా, ఆపరేటర్లు వారి పరికరాల ఆయుష్షును పొడిగించవచ్చు.
శుభ్రపరిచే షెడ్యూల్
యొక్క పరిశుభ్రత మరియు కార్యాచరణను నిర్వహించడానికి స్థిరమైన శుభ్రపరిచే షెడ్యూల్ అవసరంప్యాలెట్ బండ్లు. రోజువారీ మరియు లోతైన శుభ్రపరిచే దినచర్యలను వారి నిర్వహణ పద్ధతుల్లో చేర్చడం ద్వారా, ఆపరేటర్లు వారిని నిర్ధారించవచ్చుప్యాలెట్ జాక్స్సరైన పనితీరు కోసం అగ్ర స్థితిలో ఉండండి.
రోజువారీ శుభ్రపరచడం
రోజువారీ శుభ్రపరిచే పనులు తక్షణ సమస్యలను పరిష్కరించడానికి శీఘ్ర తనిఖీలు మరియు స్పాట్-క్లీనింగ్ కలిగి ఉంటాయి. ఆపరేటర్లు కార్యకలాపాలకు ఆటంకం కలిగించే ఉపరితల ధూళి లేదా చిందులను తొలగించడానికి ఆపరేటర్లు హ్యాండిల్స్, ఫ్రేమ్లు మరియు చక్రాలను తుడిచివేయాలి. ఈ రెగ్యులర్ నిర్వహణ శిధిలాల పేరుకుపోవడాన్ని నిరోధిస్తుంది మరియు సురక్షితమైన పని వాతావరణాన్ని ప్రోత్సహిస్తుంది.
లోతైన శుభ్రపరచడం
మరింత మొండి పట్టుదలగల ధూళి లేదా కలుషితాలను పరిష్కరించడానికి ఆవర్తన లోతైన శుభ్రపరిచే సెషన్లు అవసరంప్యాలెట్ జాక్స్. లోతైన శుభ్రపరిచే సమయంలో, ఆపరేటర్లు సమగ్ర తనిఖీ మరియు ప్రక్షాళన కోసం భాగాలను విడదీయాలి. ఈ ప్రక్రియ కదిలే భాగాల సరళత మరియు నిర్మాణ సమగ్రత యొక్క తనిఖీతో సహా వివరణాత్మక నిర్వహణను అనుమతిస్తుంది.
A కు కట్టుబడి ఉండటం ద్వారారెగ్యులర్ క్లీనింగ్ షెడ్యూల్ఇందులో రోజువారీ నిర్వహణ మరియు లోతైన శుభ్రపరిచే సెషన్లు ఉన్నాయి, ఆపరేటర్లు వారిని నిర్ధారించగలరుప్యాలెట్ బండ్లుబాగా నిర్వహించబడుతున్నాయి మరియు సమర్థవంతమైన పదార్థ నిర్వహణ పనులకు సిద్ధంగా ఉన్నాయి.
వదులుగా ఉన్న భాగాలను బిగించండి
వదులుగా ఉన్న భాగాలను గుర్తించడం
బోల్ట్లు మరియు కాయలు
నిర్వహణ కోసం ప్యాలెట్ బండ్లను పరిశీలించినప్పుడు, ఆపరేటర్లు బోల్ట్లు మరియు గింజలపై చాలా శ్రద్ధ వహించాలి. ఈ ముఖ్యమైన భాగాలు పరికరాల నిర్మాణ సమగ్రతలో కీలక పాత్ర పోషిస్తాయి. వదులుగా ఉన్న బోల్ట్లు మరియు గింజలు అస్థిరతకు దారితీస్తాయి మరియు భద్రతను రాజీ చేస్తాయిప్యాలెట్ జాక్స్మెటీరియల్ హ్యాండ్లింగ్ పనుల సమయంలో.
ఫాస్టెనర్లు
వదులుగా ఉన్న భాగాలను గుర్తించే మరో ముఖ్య అంశం ఫాస్టెనర్లను పరిశీలించడం. స్క్రూలు, రివెట్స్ లేదా క్లిప్లు వంటి ఫాస్టెనర్లను వివిధ భాగాలను భద్రపరచడానికి ఉపయోగిస్తారుప్యాలెట్ కార్ట్కలిసి. వదులుగా ఉన్న ఫాస్టెనర్లు శబ్దాలు, చలనం కలిగించే నిర్మాణాలు లేదా క్లిష్టమైన భాగాలను వేరుచేయడం వల్ల కలిగే అవకాశం ఉంది. అన్ని ఫాస్టెనర్లను సురక్షితంగా బిగించేలా చూడటానికి రెగ్యులర్ తనిఖీ అవసరం.
బిగించే ప్రక్రియ
సాధనాలు అవసరం
వదులుగా ఉన్న భాగాలను సమర్థవంతంగా పరిష్కరించడానికి, ఆపరేటర్లకు బిగించడానికి తగిన సాధనాలు అవసరం. స్టబ్బీ స్లాట్డ్ స్క్రూడ్రైవర్లు వంటి సాధనాలను ఉపయోగించడం,నట్డ్రైవర్ బ్లేడ్లు వివిధ పరిమాణాలలో.
స్థిరత్వాన్ని నిర్ధారిస్తుంది
యొక్క కార్యాచరణ మరియు భద్రతను నిర్వహించడానికి క్రమబద్ధమైన బిగించే ప్రక్రియ ద్వారా స్థిరత్వాన్ని నిర్ధారించడం చాలా అవసరంప్యాలెట్ జాక్స్. నట్డ్రైవర్ బ్లేడ్లు లేదా స్క్రూడ్రైవర్లు వంటి తగిన సాధనాలను ఉపయోగించడం ద్వారా, ఆపరేటర్లు వదులుగా ఉన్న బోల్ట్లు, కాయలు మరియు ఫాస్టెనర్లను సురక్షితంగా బిగించవచ్చు. ఈ ప్రక్రియ భౌతిక రవాణా పనుల సమయంలో అస్థిర భాగాల వల్ల కలిగే ప్రమాదాలను నిరోధిస్తుంది.
తగిన సాధనాలతో వదులుగా ఉన్న భాగాలను శ్రద్ధగా గుర్తించడం మరియు కఠినతరం చేయడం ద్వారా, ఆపరేటర్లు వాటి యొక్క నిర్మాణ స్థిరత్వం మరియు భద్రతను మెరుగుపరుస్తారుప్యాలెట్ బండ్లు, సున్నితమైన కార్యకలాపాలను నిర్ధారించడం మరియు వదులుగా ఉన్న భాగాలతో సంబంధం ఉన్న నష్టాలను తగ్గించడం.
లోడ్ సామర్థ్యాన్ని తనిఖీ చేయండి
దాని విషయానికి వస్తేప్యాలెట్ బండ్లుమరియుప్యాలెట్ జాక్స్, అర్థం చేసుకోవడంలోడ్ సామర్థ్యంసురక్షితమైన మరియు సమర్థవంతమైన కార్యకలాపాలను నిర్ధారించడానికి ఇది చాలా ముఖ్యమైనది. దిలోడ్ సామర్థ్యంసూచిస్తుందిగరిష్ట అనుమతించదగిన శక్తిఈ పరికరాలు నిర్దిష్ట పరిస్థితులలో తట్టుకోగలవు. ఓవర్లోడింగ్ను నివారించడంలో ఈ జ్ఞానం చాలా అవసరం, ఇది వైఫల్యాలకు దారితీస్తుంది మరియు భద్రతకు రాజీ చేస్తుంది.
లోడ్ పరిమితుల ప్రాముఖ్యత
ఓవర్లోడింగ్ను నివారించడం
తనిఖీ చేసే ఒక కీలకమైన అంశంలోడ్ సామర్థ్యంఓవర్లోడింగ్ను నివారించడం. ప్యాలెట్ కార్ట్ లేదా ప్యాలెట్ జాక్ను ఓవర్లోడ్ చేయడం పరికరాలపై హానికరమైన ప్రభావాలను కలిగిస్తుంది, వీల్లకు తీవ్రమైన నష్టం మరియు బరువు పంపిణీలో అసమతుల్యత. పేర్కొన్న వాటికి కట్టుబడి ఉండటం ద్వారాలోడ్ పరిమితులు, ఆపరేటర్లు ఈ సమస్యలను నివారించవచ్చు మరియు వారి పరికరాల దీర్ఘాయువు మరియు పనితీరును నిర్వహించవచ్చు.
భద్రతను నిర్ధారించడం
భద్రతను నిర్ధారించడం అనేది తనిఖీ చేయడానికి మరియు కట్టుబడి ఉండటానికి మరొక ముఖ్య కారణంలోడ్ పరిమితులు. సిఫార్సు చేసిన బరువు సామర్థ్యాన్ని మించి పరికరాలకు మాత్రమే కాకుండా, ప్యాలెట్ బండ్లను నిర్వహించే ఆపరేటర్లకు కూడా నష్టాలను కలిగిస్తుంది. నియమించబడిన వాటిలో ఉండడం ద్వారాలోడ్ పరిమితులు, ఆపరేటర్లు సురక్షితమైన పని వాతావరణాన్ని సృష్టిస్తారు మరియు ప్రమాదాలు లేదా గాయాల అవకాశాలను తగ్గిస్తారు.
లోడ్ సామర్థ్యం తనిఖీ
బరువు పరిమితులను తనిఖీ చేస్తుంది
నిర్వహణ నిత్యకృత్యాల సమయంలో, ప్యాలెట్ బండ్ల కోసం బరువు పరిమితుల యొక్క సమగ్ర తనిఖీలను నిర్వహించడం చాలా అవసరం. స్టాటిక్ మరియు డైనమిక్ లోడ్ సామర్థ్యాలను అర్థం చేసుకోవడం చాలా ముఖ్యం, ఆపరేషన్ సమయంలో గరిష్ట ఒత్తిళ్ల కారణంగా డైనమిక్ లోడ్ సామర్థ్యం తరచుగా తక్కువగా ఉంటుంది. బరువు పరిమితులను క్రమం తప్పకుండా తనిఖీ చేయడం ద్వారా, ఆపరేటర్లు వారు గరిష్ట డైనమిక్ లోడ్ సామర్థ్యాన్ని మించకుండా చూసుకోవచ్చు, తద్వారా వైఫల్యాలను నివారిస్తుంది.
లోడ్లను సర్దుబాటు చేస్తుంది
సురక్షితమైన పదార్థ నిర్వహణ పనులకు బరువు సామర్థ్యాల ఆధారంగా లోడ్లను సర్దుబాటు చేయడం అవసరం. కొత్త ప్యాలెట్లను ఆర్డర్ చేసేటప్పుడు లేదా పదార్థ రవాణాను ప్లాన్ చేసేటప్పుడు, స్టాటిక్ మరియు డైనమిక్ లోడ్ సామర్థ్యాలతో సహా లోడ్ రేటింగ్లను పరిగణనలోకి తీసుకోవడం చాలా ముఖ్యమైనది. ఈ అవగాహన వేర్వేరు బరువు సమస్యలు మరియు సందర్భాలకు తగిన ప్యాలెట్లను ఎంచుకోవడంలో సహాయపడుతుంది, భద్రతకు రాజీ పడకుండా సరైన పనితీరును నిర్ధారిస్తుంది.
రెగ్యులర్ మెయింటెనెన్స్ of ప్యాలెట్ బండ్లు, వంటివిమాన్యువల్ ప్యాలెట్ జాక్ by JUMESUNMHE, వనరులను ఆప్టిమైజ్ చేయడానికి మరియు సిబ్బంది భద్రతకు ప్రాధాన్యత ఇవ్వాలని కోరుకునే వ్యాపారాలకు వివేకవంతమైన పెట్టుబడి. సమగ్ర సర్వీసింగ్ దినచర్యను అమలు చేయడం ద్వారా, కంపెనీలు చేయగలవుపరికరాల జీవితకాలం పొడిగించండి, ఖరీదైన విచ్ఛిన్నతలను నిరోధించండి మరియు కార్యాచరణ సామర్థ్యాన్ని నిర్ధారించండి. షెడ్యూల్డ్ నిర్వహణ మాత్రమే కాదుపనికిరాని సమయాన్ని తగ్గిస్తుందిమరియు శక్తి వినియోగం కానీ పెద్ద మరమ్మతులు లేదా పున ments స్థాపన ప్రమాదాన్ని కూడా తగ్గిస్తుంది. పెరిగిన ఉత్పాదకత మరియు సుదీర్ఘ పరికరాల దీర్ఘాయువుతో సహా రెగ్యులర్ సర్వీసింగ్ యొక్క ప్రయోజనాలను నొక్కి చెప్పడం, దీర్ఘకాలంలో ఖర్చుతో కూడుకున్న కొలతగా నిర్వహణకు ప్రాధాన్యత ఇవ్వమని వ్యాపారాలను ప్రోత్సహిస్తుంది.
పోస్ట్ సమయం: మే -30-2024