నిర్వహణప్యాలెట్ జాక్స్కార్యాలయ భద్రత మరియు సామర్థ్యానికి కీలకం. రెగ్యులర్ నిర్వహణను నిరోధించడమే కాదుunexpected హించని విచ్ఛిన్నంకానీ పరికరాల ఆయుష్షును కూడా పొడిగిస్తుంది. గుర్తించడంప్రారంభంలో ధరించండి మరియు చిరిగిపోండి, ముఖ్యంగా చక్రాలపై, సురక్షితమైన పని వాతావరణాన్ని నిర్ధారించడానికి అవసరం. పరిశ్రమ అంతర్దృష్టుల ప్రకారం, నిర్వహణను నిర్లక్ష్యం చేయడం వల్ల పెద్ద గాయాలు లేదా మరణాలు వంటి తీవ్రమైన పరిణామాలకు దారితీస్తుంది. అందువల్ల, అవగాహనఎలా పరిష్కరించాలి aప్యాలెట్ జాక్మరియు తలెత్తే సాధారణ సమస్యలుప్యాలెట్ జాక్స్మరియు ఖరీదైన మరమ్మతులను నివారించడానికి మరియు సున్నితమైన కార్యకలాపాలను నిర్ధారించడానికి వారి పరిష్కారాలు కీలకం.
సాధారణ సమస్యల అవలోకనం
ప్యాలెట్ జాక్ సమస్యల అవలోకనం
భద్రత, పనితీరు మరియు దీర్ఘాయువు కోసం రెగ్యులర్ నిర్వహణ చాలా ముఖ్యమైనదిప్యాలెట్ జాక్స్. సరైన నిర్వహణ ప్రమాదాలు, గాయాలు మరియు పరికరాలకు ఖరీదైన నష్టాన్ని నివారించవచ్చు. సాధారణ నిర్వహణ తనిఖీలను నిర్వహించడం ద్వారా, వ్యాపారాలు వారి ప్యాలెట్ జాక్ల యొక్క సున్నితమైన ఆపరేషన్ను నిర్ధారించగలవు మరియు unexpected హించని విచ్ఛిన్నాలను నివారించవచ్చు. ఈ చురుకైన విధానం కార్యాలయ భద్రతను పెంచడమే కాక, కార్యకలాపాల మొత్తం సామర్థ్యానికి దోహదం చేస్తుంది.
దాని విషయానికి వస్తేప్యాలెట్ జాక్సమస్యలు, ప్రారంభ గుర్తింపు కీలకం. వారి ప్రారంభ దశలలో సాధారణ సమస్యలను గుర్తించడం ద్వారా, ఆపరేటర్లు మరింత ముఖ్యమైన సమస్యలుగా మారడానికి ముందు వాటిని వెంటనే పరిష్కరించవచ్చు. ఉదాహరణకు, సంకేతాలను గమనించడంధరించండి మరియు కన్నీటిచక్రాలపై లేదాహైడ్రాలిక్ వ్యవస్థతక్షణ శ్రద్ధ యొక్క అవసరాన్ని సూచిస్తుంది. ఈ సమస్యలను ప్రారంభంలో గుర్తించడం సకాలంలో జోక్యం చేసుకోవడానికి అనుమతిస్తుంది మరియు వర్క్ఫ్లో సంభావ్య అంతరాయాలను నిరోధిస్తుంది.
ప్యాలెట్ జాక్ ఎలా పరిష్కరించాలి
చిరునామాప్యాలెట్ జాక్సాధారణ ట్రబుల్షూటింగ్ దశలను అనుసరించడం సమస్యలకు సమస్యలకు అవసరం. ఈ దశలు సమస్యను క్రమపద్ధతిలో నిర్ధారించడం, మూల కారణాన్ని గుర్తించడం మరియు తగిన పరిష్కారాలను అమలు చేయడం. నిర్మాణాత్మక పద్ధతిలో సమస్య పరిష్కారాన్ని చేరుకోవడం ద్వారా, ఆపరేటర్లు సమస్యలను సమర్ధవంతంగా పరిష్కరించగలరు మరియు వారి పరికరాల కార్యాచరణను పునరుద్ధరించవచ్చు.
సరైన రోగ నిర్ధారణ అనేది ఫిక్సింగ్ యొక్క క్లిష్టమైన అంశంప్యాలెట్ జాక్సమస్యలు. ఏదైనా మరమ్మతులు లేదా సర్దుబాట్లను ప్రయత్నించే ముందు, సమస్య యొక్క మూలాన్ని ఖచ్చితంగా గుర్తించడం చాలా అవసరం. ఇది హైడ్రాలిక్ సిస్టమ్, ఫోర్క్స్ లేదా వంటి వివిధ భాగాలను పరిశీలించవచ్చుసరళతఏదైనా క్రమరాహిత్యాలను గుర్తించే పాయింట్లు. సమగ్ర రోగ నిర్ధారణ ద్వారా, ఆపరేటర్లు వారు కేవలం దాని లక్షణాల కంటే అంతర్లీన సమస్యను పరిష్కరిస్తున్నారని నిర్ధారించుకోవచ్చు.
సరళత సమస్యలు
సరళత ద్వారా సున్నితమైన ఆపరేషన్ను నిర్ధారించడం కదిలే భాగాల మధ్య ఘర్షణను తగ్గిస్తుంది, మీ పరికరాల జీవితకాలం విస్తరిస్తుంది. మీ కార్యాచరణను నిర్వహించడంలో సరైన సరళత కీలక పాత్ర పోషిస్తుందిప్యాలెట్ జాక్. అతుకులు మరియు కీళ్ళు వంటి కదిలే భాగాలను ద్రవపదార్థం చేయడం సున్నితమైన ఆపరేషన్ను నిర్ధారిస్తుంది మరియు క్లిష్టమైన భాగాలపై దుస్తులు మరియు చిరిగిపోతుంది.
పేలవమైన సరళత
పేలవమైన సరళతకు కారణాలు
- సాధారణ నిర్వహణ షెడ్యూల్లను నిర్లక్ష్యం చేయడం.
- తప్పు లేదా తక్కువ-నాణ్యత కందెనలను ఉపయోగించడం.
- ధూళి మరియు శిధిలాల చేరడం వంటి పర్యావరణ కారకాలు సరైన సరళతకు ఆటంకం కలిగిస్తాయి.
సరళత సమస్యలకు పరిష్కారాలు
- సరళత పౌన frequency పున్యం కోసం తయారీదారు మార్గదర్శకాలను అనుసరించండి.
- అధిక-నాణ్యత, సిఫార్సు చేసిన కందెనలను ఉపయోగించండిప్యాలెట్ జాక్స్.
- ప్రభావాన్ని నిర్ధారించడానికి కందెనను వర్తించే ముందు క్రమం తప్పకుండా శుభ్రంగా కదిలే భాగాలు.
నివారణ చర్యలు
రెగ్యులర్ సరళత షెడ్యూల్
- సకాలంలో సరళత విరామాల కోసం నిర్వహణ క్యాలెండర్ను సృష్టించండి.
- సరిపోని సరళత యొక్క ఏవైనా సంకేతాలను గుర్తించడానికి కదిలే భాగాలను మామూలుగా పరిశీలించండి.
సిఫార్సు చేసిన కందెనలు
- సరైన పనితీరు కోసం లిథియం-ఆధారిత గ్రీజులను ఉపయోగించుకోండి.
- మెరుగైన మన్నిక మరియు దుస్తులు నుండి రక్షణ కోసం సింథటిక్ నూనెలను పరిగణించండి.
మీ సరళతప్యాలెట్ జాక్కదిలే భాగాలు ఒక ముఖ్యమైన పని, దీనికి కొంత తయారీ మరియు జాగ్రత్త అవసరం. మొదట, ధూళి, ధూళి లేదా శిధిలాలను తొలగించడానికి కదిలే భాగాలను వస్త్రం లేదా బ్రష్తో శుభ్రం చేయండి. అప్పుడు, కదిలే భాగాలకు కందెనను వర్తింపచేయడానికి గ్రీజ్ గన్ లేదా స్ప్రే నాజిల్ వంటి తగిన సాధనాన్ని ఉపయోగించండి. చక్రాలు, బేరింగ్లు, ఇరుసులు, గొలుసులు, ఫోర్కులు మరియు హైడ్రాలిక్ పంప్ వంటి అత్యంత బహిర్గత భాగాలపై దృష్టి పెట్టండి.
తరువాత, ఏదైనా అదనపు కందెనను వస్త్రం లేదా కాగితపు టవల్ తో తుడిచివేయండి. చివరగా, మీ పరీక్షించండిప్యాలెట్ జాక్ఆపరేషన్ మరియు స్క్వీకింగ్, జామింగ్ లేదా లీక్ వంటి ఏదైనా అసాధారణతలను తనిఖీ చేయండి. ఈ ఉత్తమ పద్ధతులను అనుసరించడం ద్వారా మీరు మీలా చూడవచ్చుప్యాలెట్ జాక్బాగా సరళమైనది మరియు సజావుగా పనిచేస్తుంది.
తయారీదారు సూచనల ప్రకారం కదిలే అన్ని భాగాలను క్రమం తప్పకుండా ద్రవపదార్థం చేయండి; ఇది మీ పరికరాల జీవితకాలం గణనీయంగా విస్తరించేటప్పుడు ఘర్షణను తగ్గించడానికి మరియు ధరించడానికి సహాయపడుతుంది.
హైడ్రాలిక్ సిస్టమ్ సమస్యలు
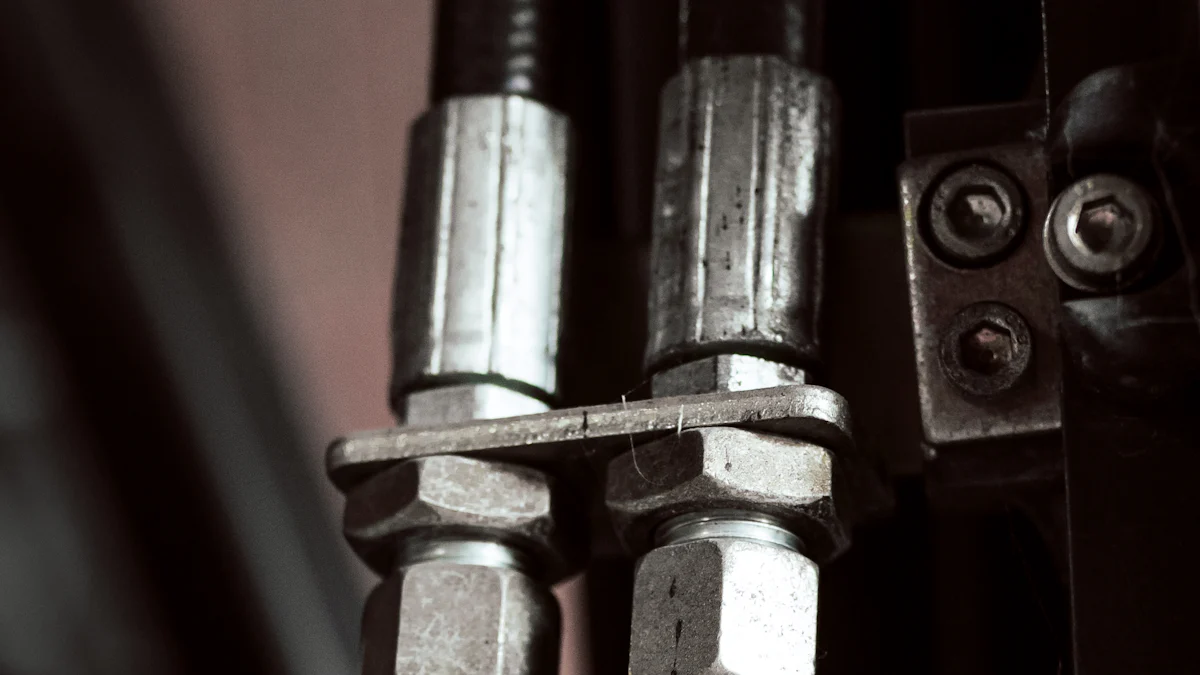
హైడ్రాలిక్ వ్యవస్థలో చిక్కుకున్న గాలి
రూట్ కారణాలను గుర్తించడానికి మరియు సమర్థవంతమైన పరిష్కారాలను అమలు చేయడానికి లిఫ్టింగ్ మెకానిజంతో సమస్యలను నిర్ధారించడానికి ట్రబుల్షూటింగ్ దశలను అమలు చేయడం అవసరం. సాధారణంట్రబుల్షూటింగ్ చర్యలు హైడ్రాలిక్ ద్రవ స్థాయిలను తనిఖీ చేయడం, నియంత్రణ కవాటాలను పరిశీలించడం మరియు సరైన పనితీరు కోసం పంప్ అసెంబ్లీని పరీక్షించడం.
- చిక్కుకున్న గాలికి కారణాలు:
- రెగ్యులర్ మెయింటెనెన్స్ షెడ్యూల్లను నిర్లక్ష్యం చేయడం వల్ల హైడ్రాలిక్ వ్యవస్థలో గాలి చిక్కుకుపోతుంది.
- నిర్వహణ లేదా మరమ్మతుల తర్వాత వ్యవస్థ యొక్క సరికాని రక్తస్రావం గాలి పాకెట్స్ కావచ్చు.
- దెబ్బతిన్న ముద్రలు లేదా కనెక్షన్లు గాలి హైడ్రాలిక్ వ్యవస్థలోకి ప్రవేశించడానికి అనుమతిస్తాయి.
- చిక్కుకున్న గాలికి పరిష్కారాలు:
- తయారీదారు మార్గదర్శకాలను అనుసరించడం ద్వారా హైడ్రాలిక్ వ్యవస్థను సరిగ్గా రక్తస్రావం చేయండి.
- సిస్టమ్ నుండి చిక్కుకున్న గాలిని సమర్థవంతంగా తొలగించడానికి తగిన రక్తస్రావం సాధనాన్ని ఉపయోగించండి.
- నష్టం యొక్క ఏదైనా సంకేతాల కోసం అన్ని ముద్రలు మరియు కనెక్షన్లను పరిశీలించండి మరియు అవసరమైతే వాటిని భర్తీ చేయండి.
దెబ్బతిందిఓ-రింగులు
జాక్ యొక్క లిఫ్టింగ్ మరియు తగ్గించడానికి హైడ్రాలిక్ వ్యవస్థ బాధ్యత వహిస్తుంది.ఏదైనా లీక్ల కోసం తనిఖీ చేయండిలేదా నష్టాలు. మీరు ఏవైనా సమస్యలను గమనించినట్లయితే, వాటిని వెంటనే మరమ్మతులు చేయండి.
- దెబ్బతిన్న O- రింగుల కారణాలు:
- సరైన నిర్వహణ లేకుండా నిరంతర ఉపయోగం O- రింగులపై దుస్తులు మరియు కన్నీటిని కలిగిస్తుంది.
- తీవ్రమైన ఉష్ణోగ్రతలు లేదా రసాయనాలు వంటి కఠినమైన పర్యావరణ పరిస్థితులకు గురికావడం ఓ-రింగులను క్షీణిస్తుంది.
- తప్పు సంస్థాపన లేదా భాగాల యొక్క అధిక బిగించడం కాలక్రమేణా O- రింగులను దెబ్బతీస్తుంది.
- దెబ్బతిన్న O- రింగుల కోసం పరిష్కారాలు:
- దెబ్బతిన్న O- రింగులపై మరమ్మతు చేయడానికి ముందు హైడ్రాలిక్ వ్యవస్థకు శక్తిని తగ్గించండి.
- మరింత హాని కలిగించకుండా తగిన సాధనాలను ఉపయోగించి దెబ్బతిన్న ఓ-రింగ్ను జాగ్రత్తగా తొలగించండి.
- భవిష్యత్ సమస్యలను నివారించడానికి సరైన ముద్రను నిర్ధారించే సరైన పరిమాణం మరియు పదార్థం యొక్క కొత్త O- రింగ్ను ఇన్స్టాల్ చేయండి.
సంభావ్య సమస్యలను ప్రారంభంలో గుర్తించడానికి హైడ్రాలిక్ యూనిట్ను క్రమం తప్పకుండా పరిశీలించడం చాలా ముఖ్యం. చిక్కుకున్న గాలి మరియు దెబ్బతిన్న ఓ-రింగులను వెంటనే పరిష్కరించడం ద్వారా, ఆపరేటర్లు వారి ప్యాలెట్ జాక్ల యొక్క సరైన పనితీరును నిర్వహించవచ్చు మరియు మరింత ముఖ్యమైన సమస్యలను తలెత్తకుండా నిరోధించవచ్చు. సరైన నిర్వహణ భద్రతను నిర్ధారించడమే కాకుండా, మీ పరికరాల జీవితకాలం కూడా విస్తరిస్తుందని గుర్తుంచుకోండి, ఇది మరింత సమర్థవంతమైన కార్యాలయ వాతావరణానికి దోహదం చేస్తుంది.
ఫోర్క్ తప్పుగా అమర్చడం
ఎప్పుడుప్యాలెట్ జాక్స్ఫోర్క్ తప్పుడు అమరికను ప్రదర్శించండి, ఇది వారి కార్యాచరణ సామర్థ్యాన్ని గణనీయంగా ప్రభావితం చేస్తుంది.నిరంతర వినియోగ సమస్యలుఈ సమస్యకు ఒక సాధారణ కారణం, అసమాన ఫోర్కులకు దారితీస్తుంది, ఇది ప్యాలెట్లను సమర్థవంతంగా ఉపాయాలు చేయడం సవాలుగా చేస్తుంది. తప్పుడు అమరిక లోడ్ యొక్క స్థిరత్వాన్ని ప్రభావితం చేయడమే కాక, కార్యాలయంలో భద్రతా ప్రమాదాలను కూడా కలిగిస్తుంది. వినియోగదారులు ప్యాలెట్ల క్రింద ఫోర్కులను సరిగ్గా ఉంచడానికి కష్టపడవచ్చు, ఫలితంగా సంభావ్య ప్రమాదాలు లేదా వస్తువులకు నష్టం జరుగుతాయి.
పరిష్కరించడానికిఫోర్క్ తప్పుగా అమర్చడం, ఆపరేటర్లు పరిగణించవచ్చుఫోర్కులను గుర్తించడంఆచరణాత్మక పరిష్కారంగా. ఫోర్కులు స్థాయి మరియు సమాంతరంగా ఉన్నాయని నిర్ధారించడానికి ఫోర్కులు సర్దుబాటు చేయడం ద్వారా, వినియోగదారులు యొక్క కార్యాచరణను మెరుగుపరచవచ్చుప్యాలెట్ జాక్మరియు లోడ్-బేరింగ్ సామర్థ్యాలను మెరుగుపరచండి. సరైన అమరిక సున్నితమైన ప్యాలెట్ చొప్పించడం మరియు వెలికితీతను సులభతరం చేయడమే కాక, అస్థిర లోడ్లతో సంబంధం ఉన్న ప్రమాదాల ప్రమాదాన్ని తగ్గిస్తుంది.
ఫోర్క్ తప్పుగా అమర్చడానికి పరిష్కారాలు
ఫోర్కులను గుర్తించడం
- ఫోర్క్ అమరికను పరిశీలించండి:ఏదైనా వ్యత్యాసాలు లేదా వంపులను గుర్తించడానికి ఫోర్కుల ప్రస్తుత అమరికను పరిశీలించడం ద్వారా ప్రారంభించండి.
- ఫోర్క్ స్థానాన్ని సర్దుబాటు చేయండి:తగిన సాధనాలను ఉపయోగించి, ఫోర్కులు సమాంతరంగా మరియు సమాన ఎత్తులో ఉన్నాయని నిర్ధారించడానికి జాగ్రత్తగా గుర్తించండి.
- పరీక్ష కార్యాచరణ:పున ign రూపకల్పన తరువాత, పరీక్షించండిప్యాలెట్ జాక్రెండు ఫోర్కులు సజావుగా స్లైడ్ అవుతాయని ధృవీకరించడానికి ప్రామాణిక ప్యాలెట్ క్రింద చేర్చడం ద్వారా.
- ఫైన్-ట్యూన్ అమరిక:సమర్థవంతమైన ప్యాలెట్ నిర్వహణ కోసం సరైన అమరికను సాధించడానికి అవసరమైతే చిన్న సర్దుబాట్లు చేయండి.
నివారణ చర్యలు
- రెగ్యులర్ తనిఖీలు:ప్రారంభంలోనే తప్పుగా అమర్చడం యొక్క ఏవైనా సంకేతాలను గుర్తించడానికి ఫోర్క్ అమరికపై సాధారణ తనిఖీలను నిర్వహించండి.
- ఆపరేటర్ శిక్షణ:సరైన నిర్వహణ పద్ధతులపై ఆపరేటర్లకు శిక్షణ ఇవ్వండి మరియు ఫోర్క్ తప్పుగా అమర్చడం యొక్క సంకేతాలను ఎలా గుర్తించాలి.
- నిర్వహణ రికార్డులు:ఫోర్క్ రియలైన్ విధానాలు మరియు తేదీలతో సహా నిర్వహణ కార్యకలాపాల యొక్క వివరణాత్మక రికార్డులను ఉంచండి.
ఈ పరిష్కారాలు మరియు నివారణ చర్యలను అమలు చేయడం ద్వారా, వ్యాపారాలు వాటిలో ఫోర్క్ తప్పుగా అమర్చిన నష్టాలను తగ్గించగలవుప్యాలెట్ జాక్స్. ఫోర్కులు సరిగ్గా సమలేఖనం చేయబడిందని భరోసా ఇవ్వడం కార్యాచరణ భద్రతను పెంచడమే కాకుండా, సమస్యలను నిర్వహించడం వల్ల కలిగే సమయ వ్యవధిని తగ్గించడం ద్వారా మొత్తం ఉత్పాదకతకు దోహదం చేస్తుంది.
ఆయిల్ పంప్సమస్యలు
కామన్ ఆయిల్ పంప్ సమస్యలు
చమురు పంపు సమస్యల కారణాలు
- రెగ్యులర్ ఆయిల్ పంప్ నిర్వహణను నిర్లక్ష్యం చేయడం వలన కాలక్రమేణా పంపు సామర్థ్యం మరియు పనితీరు తగ్గుతుంది.
- తప్పు రకం హైడ్రాలిక్ ఆయిల్ ఉపయోగించడం లేదా చమురు స్థాయిలను క్రమం తప్పకుండా తనిఖీ చేయడంలో విఫలమవడం వల్ల కావచ్చుసరిపోని సరళతమరియు పంప్ పనిచేయకపోవటానికి కారణం.
- ధూళి, శిధిలాలు లేదా తేమ కాలుష్యం వంటి పర్యావరణ కారకాలు హైడ్రాలిక్ ద్రవం యొక్క నాణ్యతను ప్రభావితం చేయడం ద్వారా చమురు పంపు సమస్యలకు దోహదం చేస్తాయి.
ఆయిల్ పంప్ సమస్యలకు పరిష్కారాలు
- రెగ్యులర్ ఆయిల్ పంప్ నిర్వహణ:
- చమురు పంపుపై సాధారణ తనిఖీలను అమలు చేయండి, లీక్ల కోసం తనిఖీ చేయడం, పీడన స్థాయిలను పరీక్షించడం మరియు సరైన చమురు ప్రసరణను నిర్ధారించడం.
- శిధిలాల నిర్మాణాన్ని నివారించడానికి మరియు సరైన కార్యాచరణను నిర్వహించడానికి పంప్ భాగాలను క్రమం తప్పకుండా శుభ్రం చేయండి.
- చమురు పంపు వ్యవస్థకు మరింత నష్టం జరగకుండా ధరించే భాగాలను వెంటనే మార్చండి.
- ఆయిల్ పంప్ వైఫల్యం యొక్క సంకేతాలు:
- గ్రౌండింగ్ లేదా విన్నింగ్ శబ్దాలు వంటి పంప్ నుండి వచ్చే అసాధారణ శబ్దాల కోసం పర్యవేక్షించండి, ఇది అంతర్గత సమస్యలను సూచిస్తుంది.
- సిస్టమ్లో సంభావ్య పనిచేయకపోవడాన్ని సూచించే పంప్ అసెంబ్లీ చుట్టూ కనిపించే లీక్లు లేదా బిందువుల కోసం తనిఖీ చేయండి.
- హైడ్రాలిక్ ద్రవ రంగు లేదా స్థిరత్వంలో ఏవైనా మార్పులను గమనించండి, ఎందుకంటే రంగు పాలిపోవడం లేదా కాలుష్యం చమురు పంపుతో అంతర్లీన సమస్యలను సూచిస్తుంది.
ప్యాలెట్ జాక్ భాగాల సమగ్రత మరియు పనితీరును కాపాడటానికి రెగ్యులర్ మెయింటెనెన్స్ అవసరం. సిఫార్సు చేసిన నిర్వహణ పద్ధతులకు కట్టుబడి ఉండటం ద్వారా మరియు ఆయిల్ పంప్ వ్యవస్థతో గుర్తించిన ఏవైనా సమస్యలను వెంటనే పరిష్కరించడం ద్వారా, ఆపరేటర్లు సున్నితమైన కార్యకలాపాలను నిర్ధారించవచ్చు మరియు వారి పరికరాల ఆయుష్షును విస్తరించవచ్చు. క్రియాశీల సంరక్షణ భద్రతను పెంచడమే కాక, గిడ్డంగి పరిసరాలలో కార్యాచరణ సామర్థ్యానికి దోహదం చేస్తుందని గుర్తుంచుకోండి.
నిర్ధారించడానికి రెగ్యులర్ నిర్వహణ చాలా ముఖ్యమైనదిసరైన పనితీరు మరియు దీర్ఘాయువుప్యాలెట్ జాక్స్. సాధారణ సేవ మరియు నిర్వహణ ప్రణాళికను అమలు చేస్తోందికార్యాచరణ సమయ వ్యవధి ప్రమాదాన్ని తగ్గిస్తుందిమరియు పరికరాల పనితీరును ఉత్తమంగా నిర్ధారిస్తుంది. రెగ్యులర్నివారణ నిర్వహణసహాయపడుతుందిunexpected హించని విచ్ఛిన్నతలను నివారించడంమరియు దీర్ఘకాలంలో సమయం మరియు డబ్బు ఆదా. సాధారణ నిర్వహణ తనిఖీలను నిర్వహించడం ద్వారా, వ్యాపారాలు గుర్తించగలవు మరియు పరిష్కరించగలవుచిన్న సమస్యలు పెరిగే ముందుప్రధాన సమస్యలుగా, ఖరీదైన మరమ్మతులు లేదా భర్తీ ప్రమాదాన్ని తగ్గిస్తుంది. గుర్తుంచుకోండి, క్రియాశీల సంరక్షణ భద్రతను పెంచడమే కాక, గిడ్డంగి పరిసరాలలో కార్యాచరణ సామర్థ్యానికి దోహదం చేస్తుంది.
పోస్ట్ సమయం: జూన్ -14-2024